Value Stream Mapping (VSM) - What and How
Origin and Inventor of Value Stream Mapping
The origin of VSM can be traced back to the Toyota Production System (TPS), a pioneering approach to lean manufacturing, developed in the 1950s by the Japanese automotive industry. The concept was formalized and popularized in the 1990s by researchers James Womack and Daniel Jones, who studied TPS in depth and applied it to other industries.When to use the VSM?
The use of VSM is recommended whenever the efficiency of a process or set of processes is at stake. It is particularly useful in a lean transformation effort, when the goal is to eliminate waste and improve overall customer value. VSM can be used to improve production processes, but also to optimize service operations or administrative processes.How to Create a Value Stream Map: Steps and Tools
Creating a Value Stream Map involves several steps:
Choosing the product or service to map: The process begins by deciding which product or service will be analyzed. This could be a specific product, a product family, or a given service.
Identifying the value stream: The value stream includes all the activities necessary to transform an input (raw materials, information) into an output (finished product or service). These activities are typically classified into value-adding activities (those that create value for the customer) and non-value-adding activities (those that do not add value).
Mapping the current state: This step involves creating a visual map of the current value stream, with details about each activity, including the time required, wait times, inventory, and more. This is a crucial step for understanding existing inefficiencies and waste.
Analyzing the current state: The team reviews the current state map to identify areas of waste, bottlenecks, and opportunities for improvement. This analysis should be thorough and involve all relevant stakeholders to gain a complete picture.
Mapping the future state: Based on the analysis of the current state, the team creates a new map representing an improved, more efficient value stream, known as the future state. This map is the team's vision of what the process should be.
Creating an action plan: The team then develops an action plan to move from the current state to the future state. This plan should include specific steps, assigned responsibilities, and a timeline for implementation.
Implementation and monitoring: Finally, the action plan is put into practice, and the process is closely monitored to ensure it meets the set goals. It's important to note that VSM is a tool for continuous improvement, which means the process doesn't end once the future state is reached. Instead, the team should continue to monitor, analyze, and improve the process on a regular basis.
Tools commonly used to make a Value Stream Map include drawing or process mapping software, as well as simpler tools like paper and pencil.
This is an example of a Value Stream Map. We can see that the value added time is 22 minutes compared to a total Lead Time of 358.5 hours.
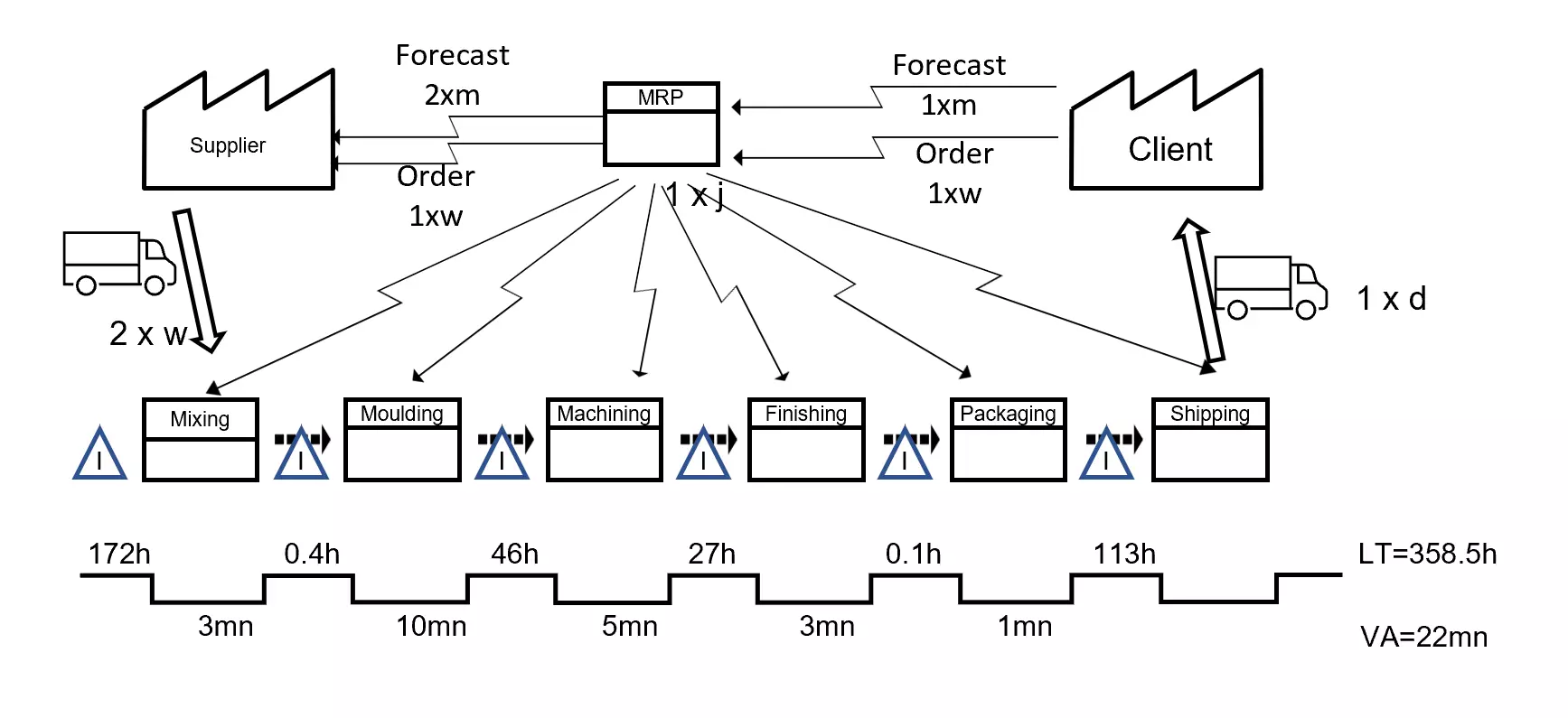
Do you need an expert to make a Value Stream Map?
Completing a Value Stream Map requires a deep understanding of the organization's processes, as well as project management and team facilitation skills. It is therefore beneficial to have someone trained in VSM to facilitate the process.That said, you don't always have to be an expert to make a Value Stream Map. Indeed, one of the main advantages of VSM is that it is designed to be a collaborative activity involving the people who do the work. So while VSM-specific training can be helpful, the key is for the facilitator to be able to assemble and guide a team, understand and visualize processes, and ask the right questions to identify opportunities. of improvement.
It is important to note that if the organization is large or if the process to be mapped is complex, it may be beneficial to hire an external facilitator or a consultant specialized in lean management to help achieve the VSM. These experts typically have significant experience conducting VSM in a variety of environments and can bring a useful external perspective to identify wastes and opportunities for improvement.
The benefits of VSM
VSM offers many benefits. It helps organizations focus on activities that create value, eliminating waste. It offers a clear and complete vision of the processes, which makes it possible to identify the problems and the opportunities for improvement. The VSM also promotes employee engagement, allowing them to understand how their work fits into the overall value stream.Difficulties with VSM and how to overcome them
Although VSM is a powerful tool, it also presents challenges. For example, getting commitment from everyone in the organization can be difficult, especially if some perceive VSM as a threat to their work. Additionally, the mapping process can be complex and requires proper training and expertise.These difficulties can be overcome in several ways. First, it is critical to clearly communicate the goals and benefits of VSM to everyone in the organization. Second, proper training can help overcome technical difficulties with mapping. Finally, management support is crucial to ensure the commitment necessary for the success of the VSM.
Conclusion
In conclusion, Value Stream Mapping is a valuable tool for improving efficiency and quality in organizations. Despite the challenges it may present, its potential benefits make it a wise investment for any organization looking to optimize its processes and maximize its value for the customer.
When you subscribe to the blog, we will send you an e-mail when there are new updates on the site so you wouldn't miss them.
Comments